Cold stamping process in paper packaging box
Cold stamping is a technology that transfers hot stamping foil to the substrate with the help of a printing plate and a UV curing adhesive. Compared with the traditional hot stamping technology, the whole process without heating, also do not need special metal hot stamping plate, so can save a lot of energy, is a new technology in line with the requirements of green environmental protection, cold stamping technology according to the process can be divided into dry laminating and wet laminating type two.
- dry laminating type The coated UV adhesive is cured first and then hot stamping. The main process steps are as follows:
1) Printing UV adhesive on drum substrate;
2) curing U ⅴ adhesive;
3) is the use of pressure roller to hot stamping foil and printing material composite together;
4) it is to peel off the excess hot stamping foil from the printing material, only in the part of the hot stamping foil coated with adhesive transfer to the printing material, get the required hot stamping text.
It is worth noting:
Dry laminating cold stamping process, the curing of UV adhesive should be carried out quickly, but not completely curing, to ensure that the curing still has a certain viscosity, so as to bond with hot stamping foil well together.
After coated with UV adhesive, first hot stamping and then curing UV adhesive, the main process steps are as follows:
1) Printing free radical UV adhesive on drum printing material.
2) composite cold stamping foil on the printing material.
3) the free radical UV adhesive curing, because the adhesive at this time sandwiching between hot stamping foil and printing material, UV light must be through hot stamping foil to reach the adhesive layer.
4) the hot stamping foil from the printing material, and the formation of hot stamping on the printing material.
To be clear:
Wet laminating cold stamping process with free radical UV adhesive to replace the traditional cationic UV adhesive;
The initial viscosity of UV adhesive is strong, no more viscosity after curing;
Hot stamping foil aluminum plating layer should have a certain light transmittance, to ensure that UV light can pass through and trigger UV adhesive curing reaction.
Wet laminating cold stamping process can be used on the printing machine wire hot stamping metal foil or holographic foil, its application is more and more widely. At present, many narrow-format box and label flexo printers have this capability.
Advantages and disadvantages of cold stamping
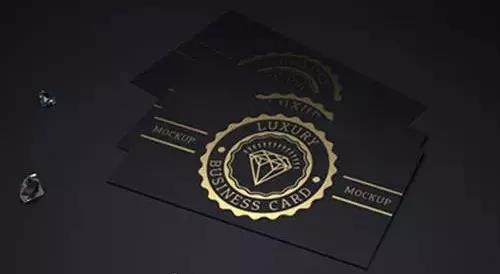
Compared with the traditional hot stamping technology, cold stamping technology has outstanding advantages, but because of the inherent process characteristics of cold stamping, it must have shortcomings.
1) Cold stamping without special hot stamping equipment, and offset printing, flexo printing, gravure printing and other equipment to achieve line production.
2) cold stamping does not need to make expensive metal hot stamping plate like hot stamping, but also avoid the pollution caused by the metal hot stamping plate production process. Cold stamping can use ordinary flexible plate, not only fast plate making, short cycle, but also reduce the production cost of hot stamping plate. This can make full use of cold stamping technology in the short plate printing cost advantage actively develop plate hot stamping business. At the same time, with environmental protection and energy saving advantages, cold stamping technology to replace the traditional hot stamping technology is also a good choice for enterprises to implement green printing, production mode reform.
3) Compared with hot stamping, cold stamping technology has the advantages of fast hot stamping speed and high precision. The back of the anodized hot stamping foil used in the traditional hot stamping process is coated with hot melt adhesive. During hot stamping, the hot melt adhesive is melted by the temperature and pressure of the hot stamping plate and the transfer of hot stamping foil is realized. And cold stamping adhesive is the use of UV curing principle, curing time is significantly shortened, so it has a faster hot stamping speed.
4) a wide range of substrate printing. Cold stamping can rely on adhesive and pressure at room temperature to transfer foil, without special adjustment and control of hot stamping temperature like hot stamping. Therefore, cold stamping technology is not only suitable for hot stamping paper, cardboard and other ordinary substrates, for the deformation of film materials, thermal sensitive materials, in-mold labels can also be applied. This makes cold stamping technology unique in daily chemical label, wine label, food label and other label applications.
5) It is easier to realize stamping before printing. Hot stamping process is the hot stamping on paper, cardboard or plastic film before printing and glazing. Cold stamping process pressure is light and very uniform, cold stamping pattern surface is smooth, at the same time, cold stamping operation difficulty is low, high efficiency, can achieve wire production, so in the cold printing pattern surface using high transparent ink printing, can get colorful, kaleidoscopic gold effect.
1) The process is complex and has technical obstacles
Cold stamping is the use of printing adhesive method transfer hot stamping foil, hot stamping patterns on the surface of the printing material fastness is not high, the hot stamping products usually need to be coated or glazing for secondary processing protection, making the process complicated. And, because of the poor leveling of UV adhesive, if there is no smooth and uniform spread, may lead to hot stamping foil surface diffuse reflection, affect the color and gloss of hot stamping text, and then reduce the beauty of the product.
For a long time, one of the key factors restricting printing enterprises to invest in cold stamping equipment is that the speed of hot stamping should be consistent with the speed of printing after the line, and it can not be used to save hot stamping foil like hot stamping equipment, which is bound to cause great waste of hot stamping, and then lead to cost increase. Although in recent years, some printing equipment manufacturers have introduced cold stamping modules with step function, most of them are at the expense of printing speed, and have not reached the maximum utilization of hot stamping foil.
2) Hot stamping quality to be improved
Compared with hot stamping, cold stamping in the graphic metal effect and hot stamping surface flatness as hot stamping. This is mainly determined by the principle of the two technologies: hot stamping stamping process similar to the iron ironing, hot stamping surface natural bright and smooth; Cold stamping technology mainly relies on adhesive adhesion stripping, stripping hot stamping foil surface effect is the final effect. As can be imagined, the surface of the flatness of nature as hot stamping. In addition, cold stamping products in other follow-up processing, usually there will be hot stamping pattern hair, paste version, text gradient is not smooth or small dot loss phenomenon, hot stamping patterns because of insufficient fastness, easy to fall off after friction, hot stamping patterns easy to produce linear wrinkles and other quality defects.
- The development of cold stamping
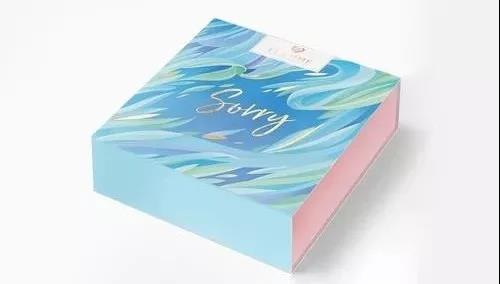
Although cold stamping technology has attracted much attention, but at present the domestic packaging and printing enterprises are still cautious about it. There is still a long way to go for cold stamping technology to be widely used in China. The main reasons can be summarized as follows :01 Cognitive deficiency
Many printing enterprises only use the hot stamping process as a separate post-press finishing process, and do not continue to print on the foil to pursue other effects. For example, after the first hot stamping, the use of four-color overprinting, can produce dazzling metal color and lustre.
Cold stamping to obtain greater development, technology must be more mature, the process must be more stable. In order to improve the adhesive, cold stamping foil and substrate matching degree at the same time, to find ways to reduce the dependence of fine cold stamping products on high-quality hot stamping foil and high quality adhesive. And, should further expand sheetlet offset line hot stamping technology suitable models.
Investment cost is too high
Equipment investment cost and consumables use cost. Hot stamping technology in the domestic hot stamping market has been applied for a relatively long time, has formed a complete and mature system including equipment, materials, technology, operators and technical support, the market foundation is firm, so in the short term its mainstream position is difficult to shake. By comparison, cold seal technology, due to the time of launch late, all aspects of the matching and the technology is not mature enough, such as cold printing equipment on the market at present, the number of suppliers of cold foil and adhesives co., LTD., choice is small, and most dependent on imports, making use of cost and supply problems, which makes the most was not very profitable more reluctant to packaging printing enterprises Take the initiative to apply the new technology.
Market demand is the key to the promotion and application of cold stamping technology, but at present the end user's understanding of cold stamping technology is far from enough. Although, in general, cold stamping quality is not as hot stamping, but some cold stamping sample ordinary customers can not tell whether it is using cold stamping method to achieve. Therefore, there will not be many customers will pay attention to the printing is what kind of hot stamping process, they pay more attention to the final effect of hot stamping, and cold stamping in hot stamping fine lines and words have a good performance. In order to realize the growth of cold stamping market share, improve customer awareness of cold stamping technology, expand market demand is the key.